Sensors
Ultra-high bandwidth optomechanical gyroscope
Our goal is to design an optomechanical gyroscope based on a SiN integrated Mach-Zehnder Interferometer (MZI) platform, which operates at sub-megahertz with the sense mode slightly shifted from the drive mode to improve system robustness while exhibiting a much-improved sensitivity and noise performance.
The reliability and sensitivity of micromachined gyroscopes are primarily determined by their structural properties. There is a trade-off between system stiffness and the out-of-plane motion of the proof mass, hence, the main challenge is to design a robust gyroscope while maintaining a minimum detectable signal that is above the noise floor. Conventional micro-machined gyroscopes attain the possible maximum response gain by matching the drive and sense mode resonant frequencies, which makes dynamical system parameters get perturbed easily by any environmental variations. To achieve a stable response, the drive and sense mode resonant frequencies of our gyroscope are separated by mechanical designs. Thus, if the gyroscope is operated at drive mode resonance, the frequency variation will have a reduced effect on the sense mode response amplitude. This provides a higher tolerance for fabrication imperfections and fluctuations in temperature and stresses [1].
The principle of operation of the gyroscope is to detect a linear sense-mode response based on the drive oscillation to a sinusoidal Coriolis force in the presence of an angular-rate input in the y-direction. The induced Coriolis force is orthogonal to the drive-mode vibration and the proof mass is free to oscillate in two orthogonal directions: the drive mode along the z-axis and the sense mode along the x-axis as shown in Fig. 1.
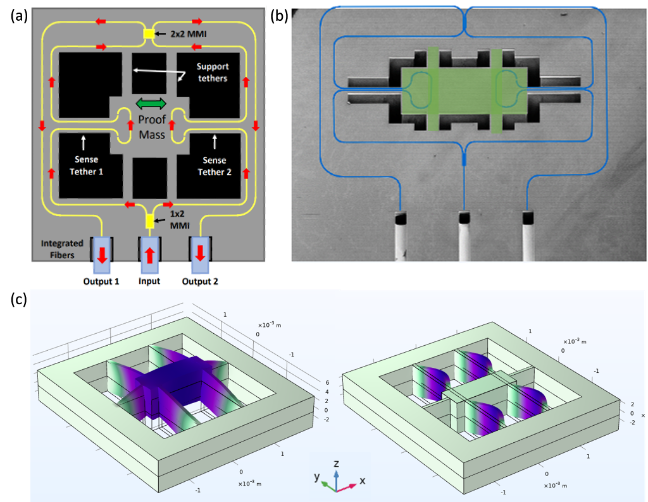
Fig.1(a) Schematic of a gyroscope integrated with MZI. (b) SEM image of the previous MZ accelerometer device, the green region representing the Aluminum-Nitride-based piezoelectric actuator that vibrates the gyroscope. (c) 3D gyroscope FEM simulation layout: out-of-plane drive mode (left) and in-plane sense mode (right).
The integrated SiN MZI platform allows optomechanical coupling from the mechanical deformation induced by the proof mass motion, converting the differential strain into optical phase change as a result of the 2×2 interference variation [2]. This integrated photonic device achieves a sensitive strain measurement in the optical domain, its response sensitivity is defined as the change in output power over the harmonic motion in the sense mode direction.
For the next steps, this approach will be implemented on bulk-micromachined prototypes to have a rigid structure and be surface micro-machined. The interferometric calibration of angular and linear translations and the system characterizations of this device will be experimentally demonstrated. The environmental noise sources that lead to bias and scale factor instability and ultimately navigational error will be evaluated.
REFERENCES
[1] Acar, Cenk, and Andrei M Shkel. MEMS Vibratory Gyroscopes: Structural Approaches to Improve Robustness. 1. Aufl. ed., Springer Science Business Media, 2009.
[2] Dominguez, Daniel, et al. “Megahertz Bandwidth Bulk Micromachined Optomechanical Accelerometer With Fiber Optical Interconnects.” 2021 IEEE International Symposium on Inertial Sensors and Systems (INERTIAL), 2021, pp. 1–4.