Laser stress figuring
Controlling low spatial frequency height errors during fabrication of thin substrates is difficult due to their low stiffness. Furthermore, many reflective coatings exhibit difficult-to-predict stress that bends these compliant substrates after material-removal processes have already figured them. Stress-based figuring, on the other hand, can accurately correct figure errors with magnitudes of tens of micrometers, even after coatings have been applied.
Focusing an ultrashort pulsed (USP) laser into transparent materials results in nonlinear absorption and subsequent extreme heating and cooling to generate stress. We are developing a process to control this stress within glass mirror substrates to correct figure errors.
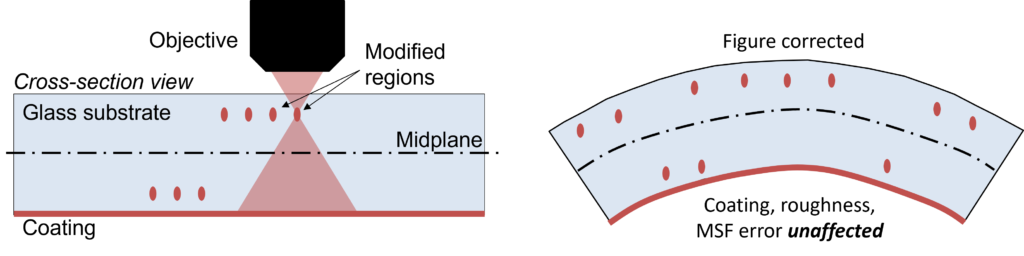
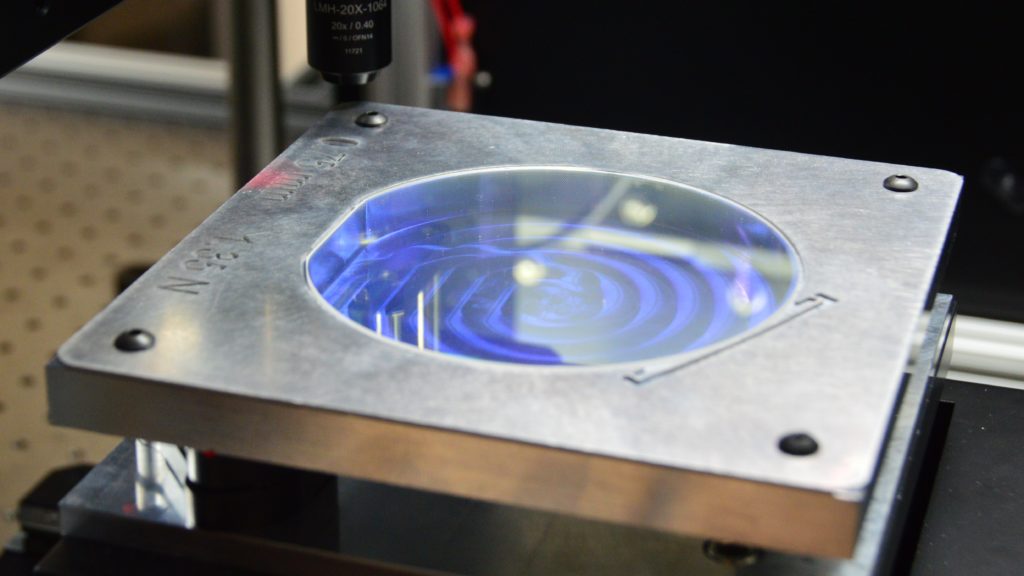
Controlling three components of in-plane stress is necessary for full-aperture accurate figure correction. We have developed procedures and software to implement this. Our recent results show consistent reductions from 3.6 μm RMS figure error (first 6 orders of Zernike polynomials) to <0.05 μm RMS in 2-3 correction cycles. We are working to improve this further.
Publications
B. D. Chalifoux, I. J. Arnold, K. A. Laverty, “Figure correction of glass mirrors using ultrafast lasers to generate controllable stress,” OSA Optical Design and Fabrication Congress, OW4B.2 (2021).